COMPLETE MAKE-OVER OF THE GATE PROCESS
Camco has been MPET’s technology partner since its relocation of the Delwaidedock to the Deurganckdock in 2016. The relocation strategy responded to increasing vessel size and offered more opportunities for process improvement and for further growth. The gate process at the previous location was less automated. Gate-Out had OCR, but Gate-In was still in full manual operation, with all manual lanes, problem & admin desks and an important overall administration. The relocation was the perfect occasion to completely rethink and automate the Gate process: A Truck Appointment System (TAS), visual OCR Gate-In and Pre-Gate-In with automated Gate process were implemented. Gert Bulté, MPET Terminal Manager: “The new process design also allows more container ground-slots which reduces need for truck parking at the admin complex and safer tallying and physical checks at the In-Gate. Today, only the exceptions are processed manually.”
A TRUCK APPOINTMENT SYSTEM FOR MANAGING THE TRUCK-FLOW
One of the process changes for speeding up the gate process, was the implementation of an in-house developed Truck Appointment System (TAS). The terminal, trucking companies and truck drivers benefit from the TAS: For MPET, the TAS is a great tool for managing transparent time-slots for the terminal’s 24/5 schedule. The tool contributes significantly to managing peaks but also facilitates yard housekeeping. Getting trucking companies and drivers on board required communication and training, but with upfront truck, driver and cargo registration, the terminal’s users were able to reduce the hassle at the gate and significantly improve their truck-turnaround.
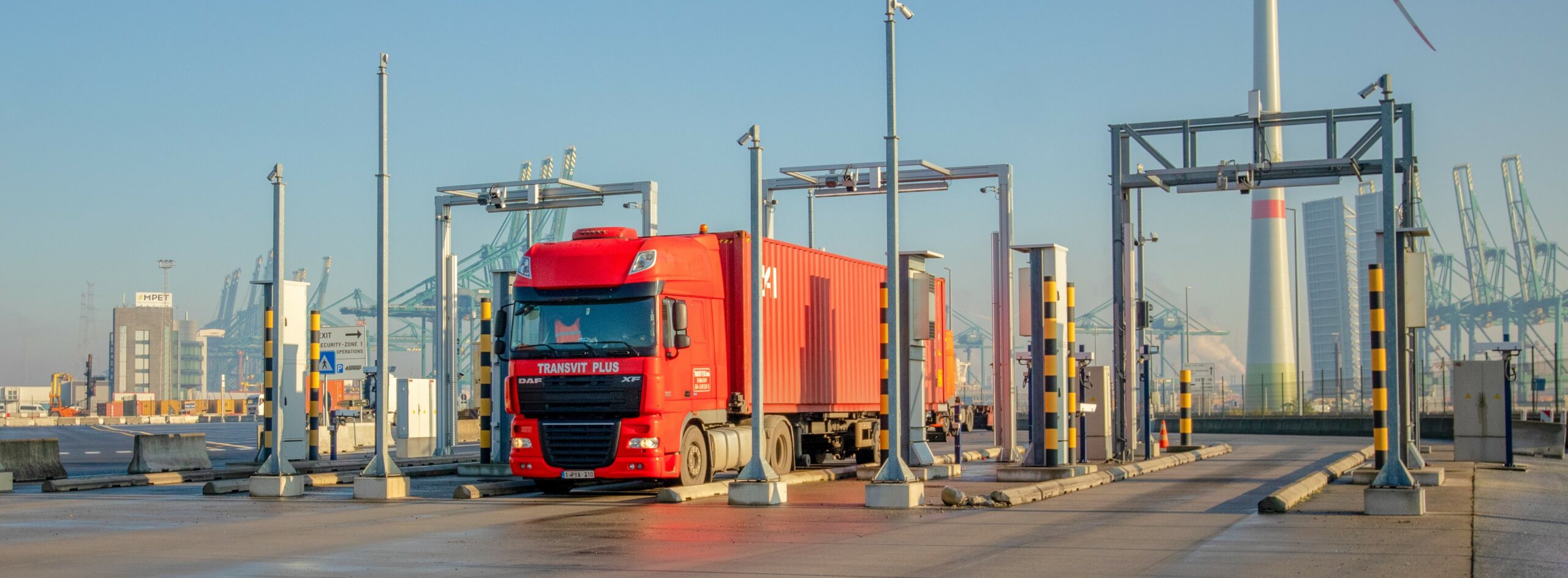
SIMPLIFIED PROCESS AT THE INTERCHANGE ZONE
Prior to the relocation, also the processes at the Interchange Zones required extensive input from truckers, delaying turnaround. With the Truck Appointment System and the Camco interchange kiosks put in place, the admin hassle for the driver is replaced with a simple badge swipe. With reduced paperwork, now only one admin point is needed for each two container transfer lanes. Apart from faster turnaround, the Camco Interchange Kiosks contribute to increased safety since its process design requires drivers to stay in a safety zone during container pick-up and drop-off: drivers need to hold down the safety button during the complete container transfer process.
“With faster truck turnaround times and increased safety, we really have turned trucking companies and drivers into ambassadors for the new gate and Interchange Zone processes”.
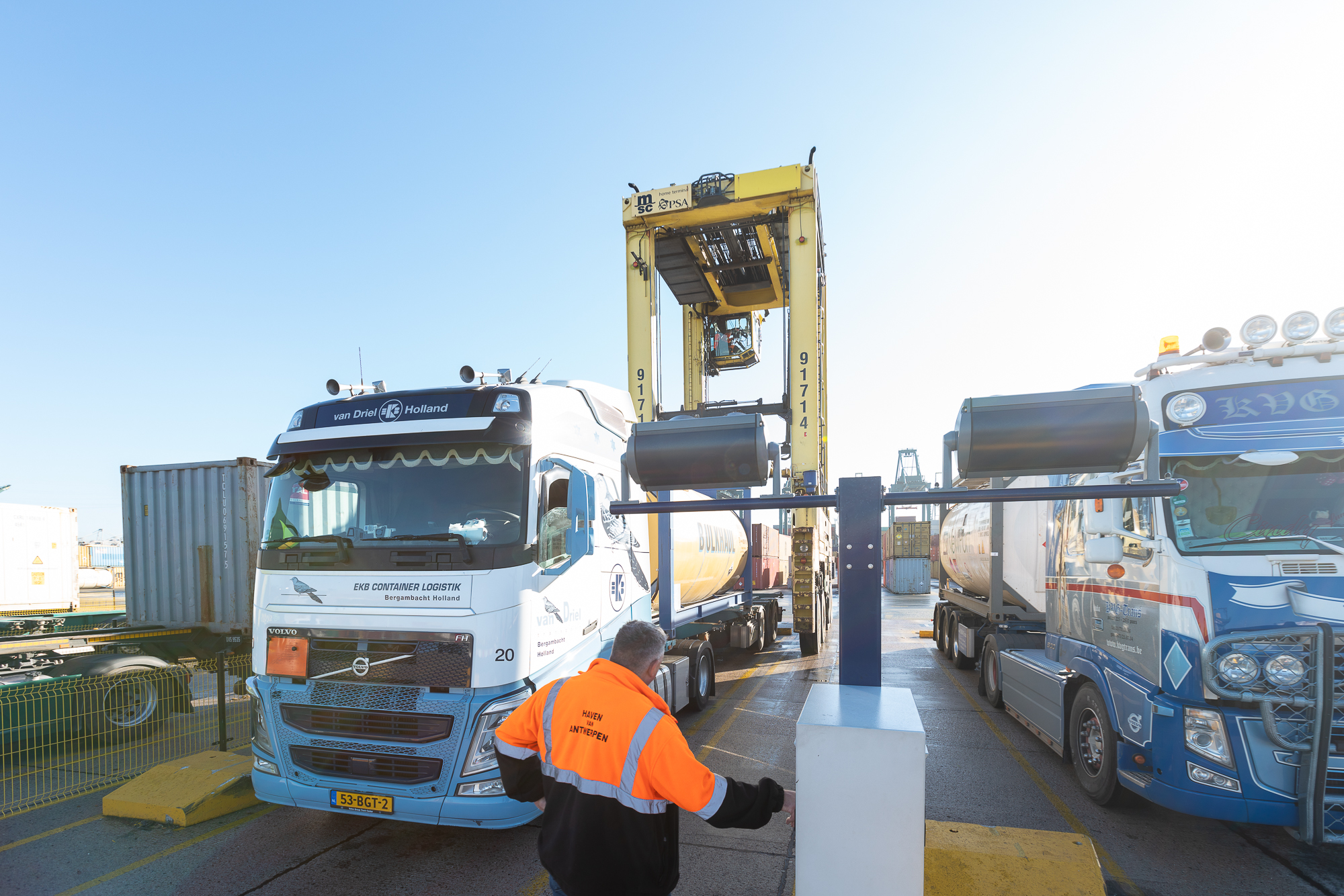
Increased safety: the truck drivers needs to push a safety button in the interchange zone during the complete transfer process.
PHASED ROLL-OUT OF THE NEW GATE DESIGN
Moving the terminal to the left bank was the world’s largest container terminal relocation project. This made a very thorough phasing of rollout necessary. Visual, Pre-and Gate-In were phased later on as this required substantial changes in the process organization and needed more testing. However, gate automation was key in aiming for a fully automated truck cycle. A careful capacity assessment led to a 3-step Gate-In design including 3 Truck OCR-In lanes, 12 Pre-Gate-In lanes and 13 Gate-In lanes for avoiding bottlenecks and queuing at the Gate-In complex, which processes more than 3000 trucks daily at peak times.
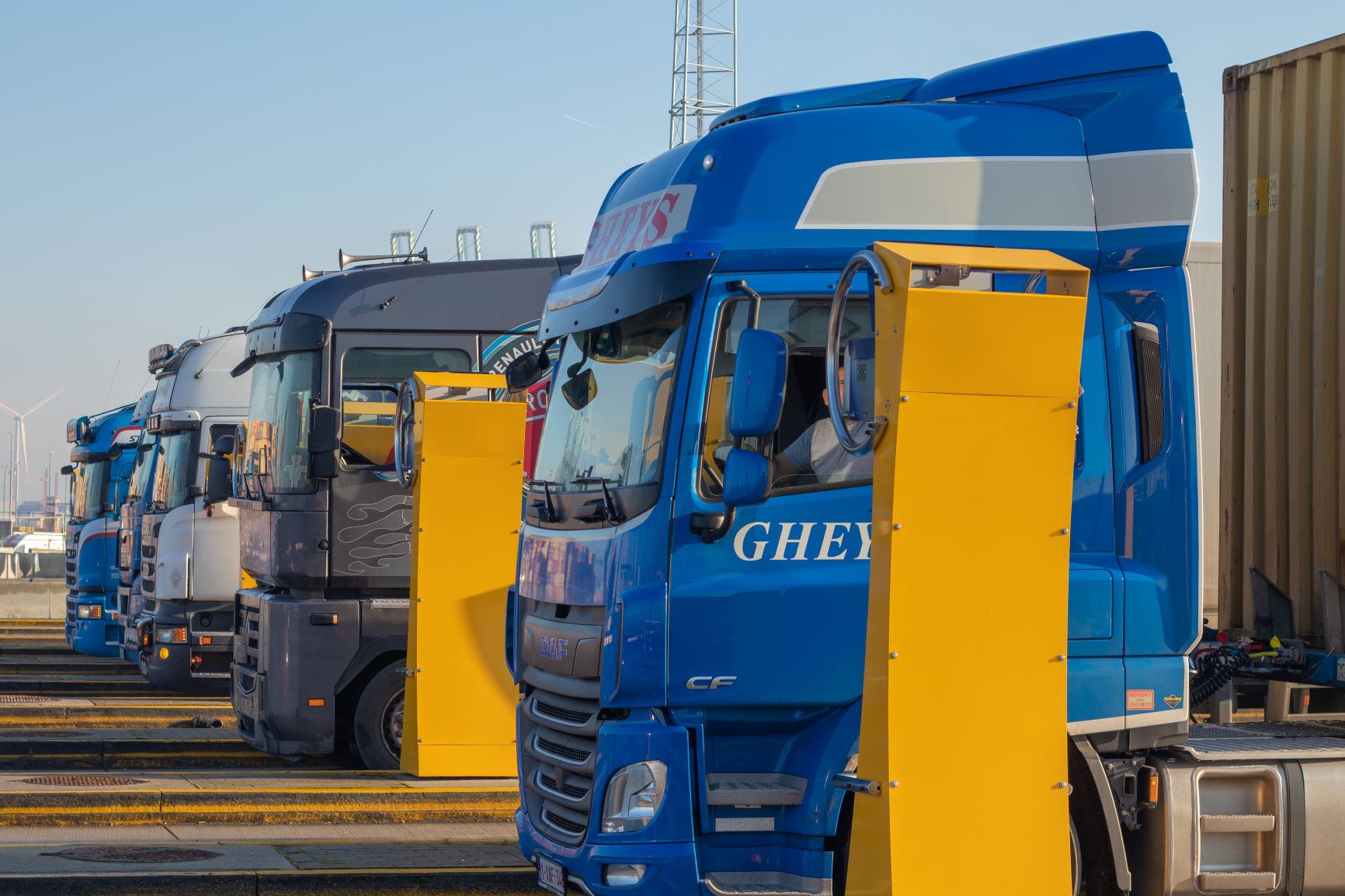
With 12 Pre-Gate kiosks, 20 Self-Service Desk kiosks, 5 OCR Gate In portals and 15 Gate-In kioks lanes, bottlenecks and queuing are a thing of the past.
ALL 41 CRANES EQUIPPED WITH DISRUPTIVE CAMCO BOXCATCHER STS CRANE OCR
Another cornerstone of the terminal automation strategy implied STS crane automation. Prior to the terminal relocation, each of the 41 STS crane had a tallyman in the gang operating a handheld terminal manually completing container ID & ISO code, IMDG, seal presence and max gross weight. In search of a robust OCR crane solution, different routes had been assessed. A PTZ camera system soon seemed not a viable solution, fixed CCTV cameras were considered for a moment, but this solution would require a substantial set of cameras per crane to avoid blind spots, a complex system integration and possible significant downtime during camera maintenance. Moreover, lack of proven solutions in the container handling industry was an additional drawback. The risk assessment for both alternatives soon turned negative.
With only two dynamic cameras per crane, Camco BoxCatcher system came out as the best STS crane automation solution. The Camco BoxCatcher disruptive design composed of a flying camera system hoovering over vertical rails fixed onto the crane frontal legs, enabling the capturing of every container, whatever the spreader flight path. With the Camco solution, only two BoxCatchers per crane are required for container identification providing 360° images of each box, be it 20, 40 or 45ft containers.
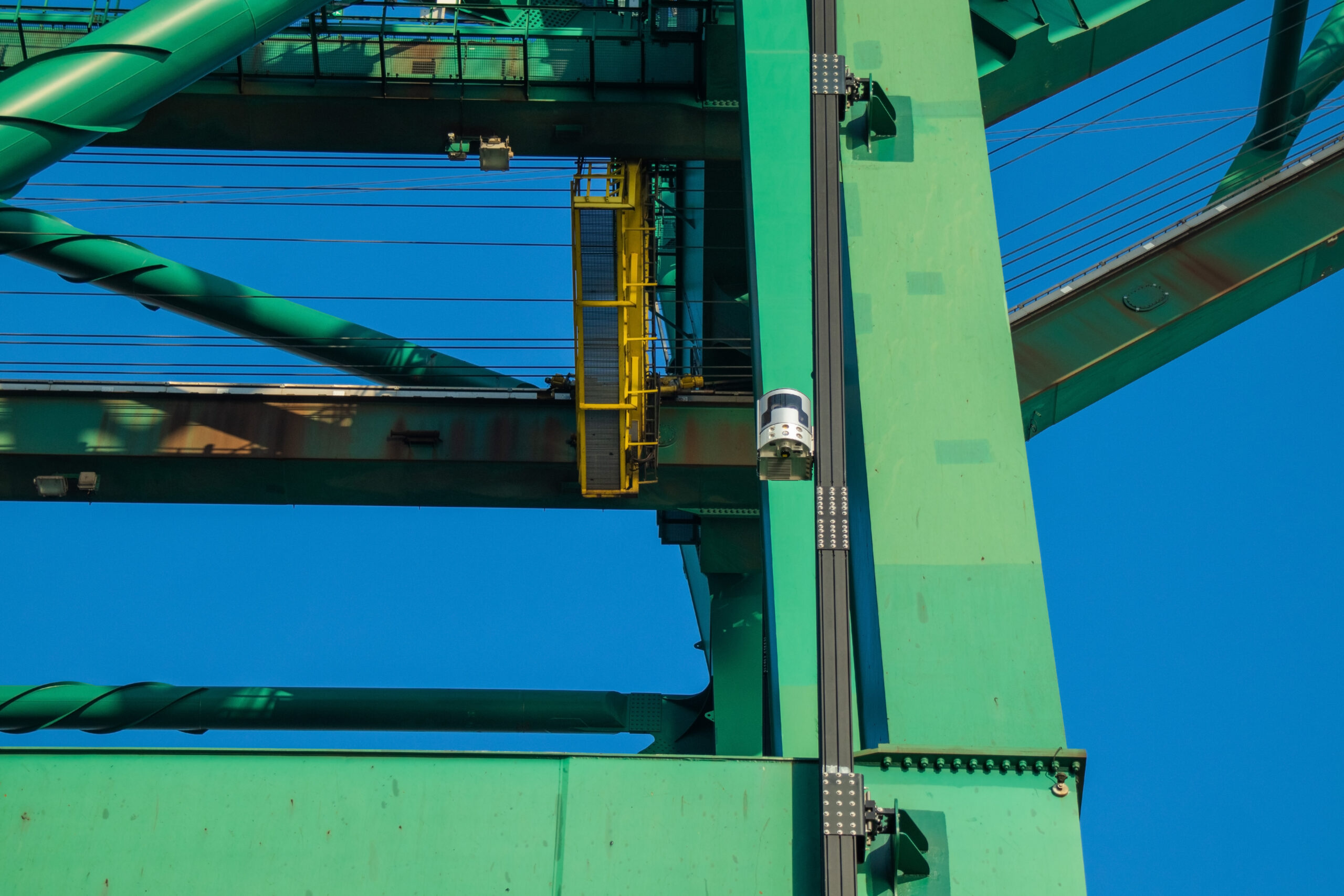
With the BoxCatcher linked to the crane PLC, and taken into account the container flightpath, the BoxCatcher system travels along the vertical rails to the exact location for container identification and condition recording. On each of the 41 cranes, 2 BoxCatcher identify each container and take 360° pictures for condition recording.
ACCURACY OF INFORMATION
The sooner information is available, the sooner real-time planning processes can start. It goes without saying that the information needs to be accurate and reliable. For any terminal, it should be a target to put every box in the right position and not touch it again until it leaves the terminal. Accuracy of information is a key parameter to reduce planning errors, avoid re-handles, housekeeping or shifting moves and idle moves. Fewer moves mean less fuel consumption, less wear and tear of the handling equipment and a higher productivity rate on the yard.
SAFETY FIRST – REMOTE EXCEPTION HANDLING
Apart from increased performance, Camco‘s STS crane solution contributes to more safety under the crane. Tallymen now let the crane OCR do the work and only focus on exceptions from a remote and safe office. “The BoxCatcher crane software application integrates seamlessly with the terminal TOS via the PSA middleware ConEqTer that serves as the tallyman exception portal. The primary OCR process with connection to the crane PLC is run by Camco”.
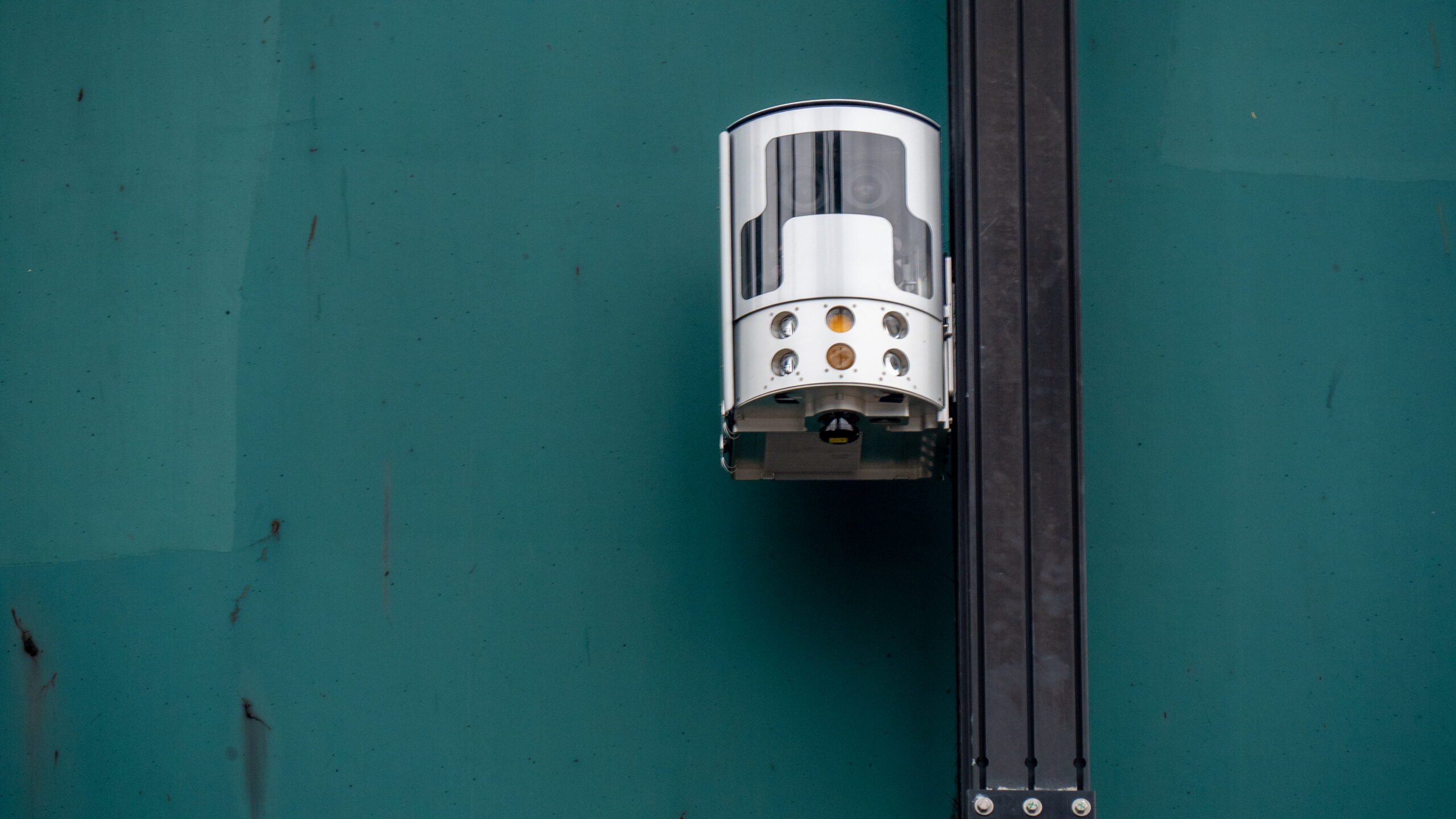
ORGANIZING BOXCATCHER INTALLATION
Implementing 41 cranes with two BoxCatcher systems each was quite a challenge. The joint project team was well prepared and had learned from an earlier BoxCatcher implementation project at PSA Antwerp. Each party focused on its expertise. Camco organized to have the 42-meter rails assembled beforehand on a dedicated warehouse on-site. Hoisting the rails took place in scheduled windows of 2 by 2 cranes. This way, Camco and MPET managed to install and commission two cranes in just a 2-3-day time window. Aware of the many challenges, the MPET team succeeded well in taking into account all aspects of the operation without disrupting operations:
- Maximum preparation of the cranes during normal maintenance windows: cabling, electrical cabinets, industrial PCs, IT network testing etc.
- Detailed planning of installation weeks: hoisting, fiber cable pulling
- Relying on the in-house partner for STS welding works for greater efficiency
- Avoiding aerial/boom lifts and relying on specialized STS crane climbing team.
- Getting stakeholders on-board with an extensive training and communication roll-out.
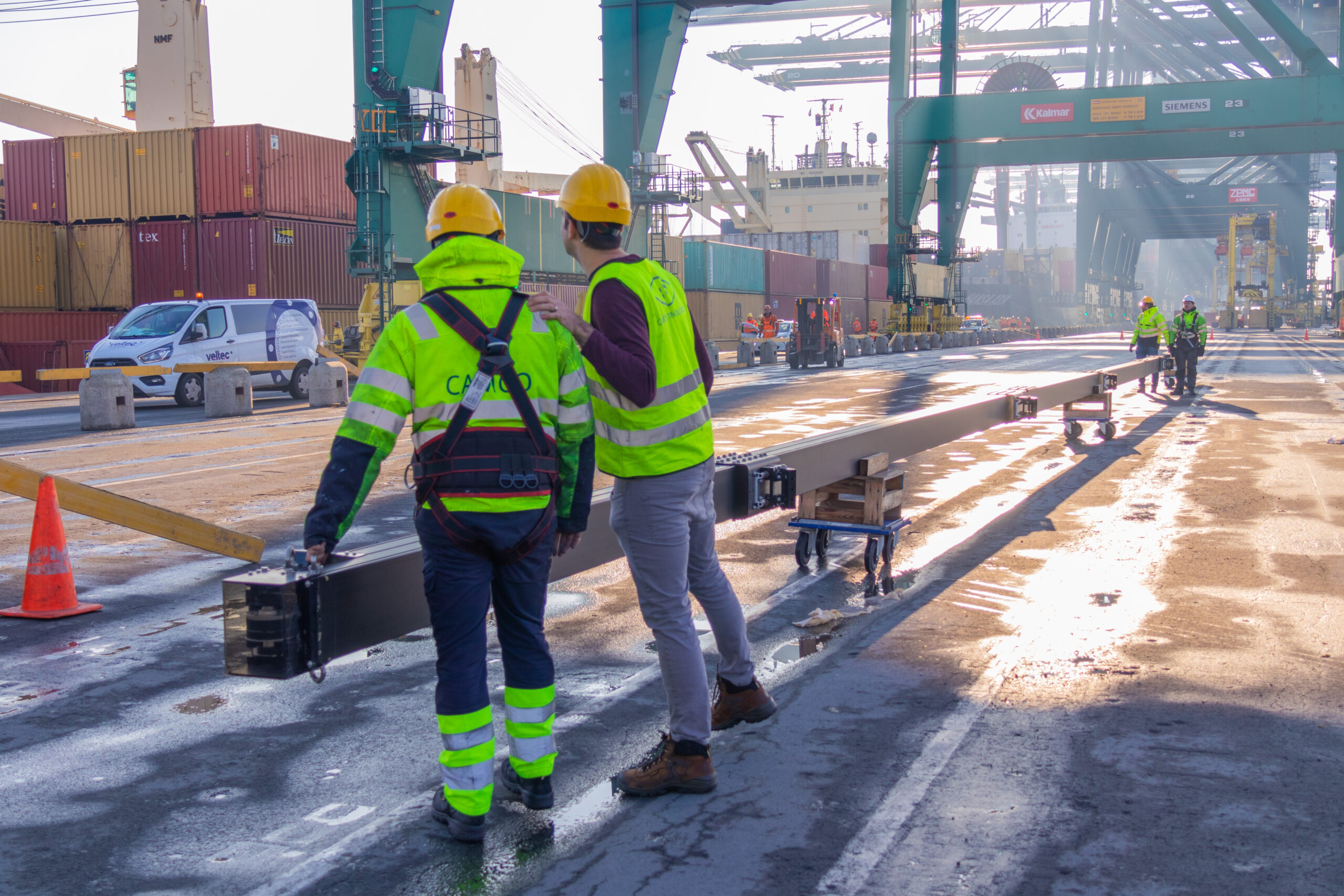

FROM DESIGN TO INSTALLATION IN JUST 12 MONTHS
“With 82 BoxCatcher installed on 41 cranes in less than one year, and minimal operational impact in a record year of handling 7.5+ million TEU in Europe’s single largest container terminal with the biggest crane density, this project has been very successful to say the least”.
Short communication lines between the MPET and Camco project team contributed to its success. Of course, as with every similar scale project, it’s easy to pinpoint improvements after implementation or call for earlier issue identification avoiding unnecessary surprises underway. But then, project business is project business and the unexpected never far away.
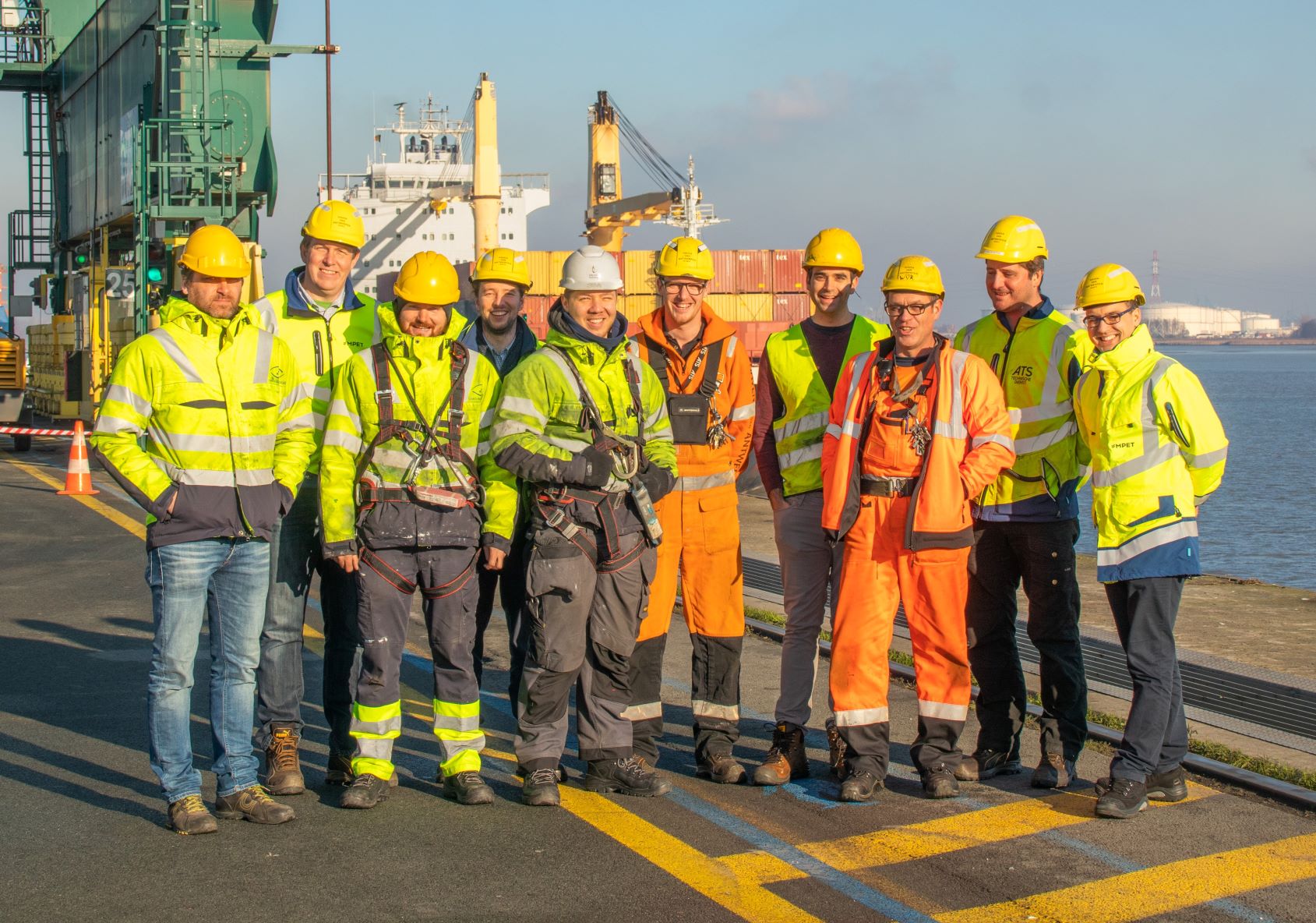
A temporary on-site Camco workshop and specialized MPET STS crane welding and climbing team contributed to speed and agility during installation.
KEY-DRIVERS FOR CHOOSING CAMCO
When selecting the appropriate solution, system performance remained the key driver. Accuracy is paramount as it determines the exception rate of the automated process. In the end, the exception rate determines the business-case for implementing the solution. Camco has a proven track record of integrated terminal automation solutions including complete gate automation systems and Crane OCR. Working with a single experienced integrator, who carries end-to-end responsibility and provides support, definitely limits the number of different systems interfacing with each other.
The complete automation project includes a substantial quantity of hardand software. Good upfront SLA contract clauses and a daily/weekly liaising between the MPET Service Management Department and Camco Maintenance & Support team is key for maximum uptime and performance.
We were looking for a proven and reliable partner/integrator to build a long relationship extending the project lifespan. Since we operate 365-24/7, we require similar support. A proven solution with low maintenance footprint and high mean time between failures (MTBF) was key. Camco stood out for its holistic approach, designing a tailor-made solution, including post-project support.
ON-BOARDING OF STAKE-HOLDERS
All internal and external stakeholders were involved in the change process: customers, unions, tallymen and the terminal management. Tallymen received training for their new exception handling role. Today, they can handle exceptions safely from a desk instead of doing the same tasks in dangerous conditions right under the crane. Customers such as trucking companies and independent truck drivers have also been informed about the changes well before, and now embrace the automation process since it significantly reduces the paper hassle and endless waiting at the gate and Interchange Zones.
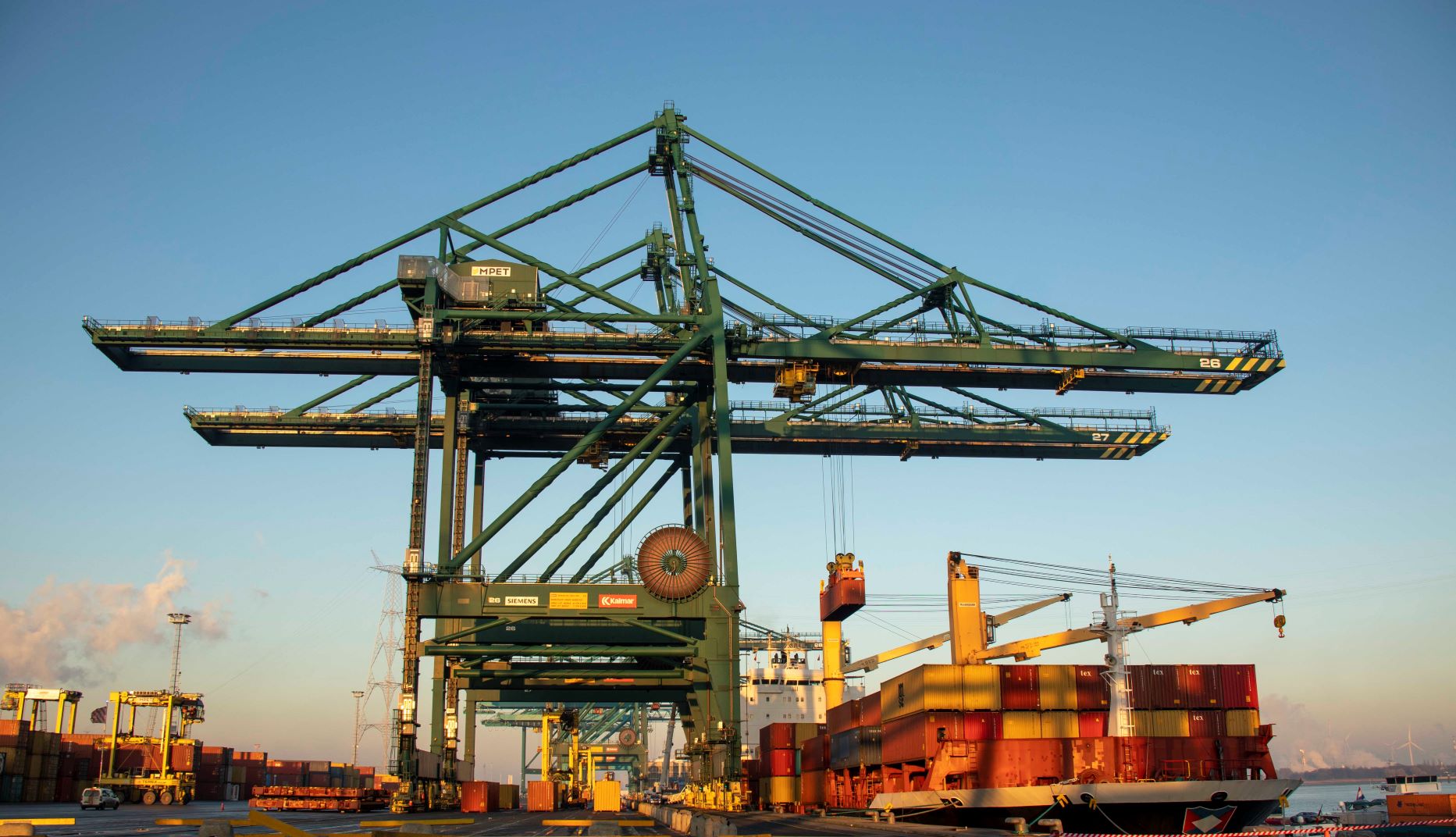
In the end, it comes down to maximum tally staff protection, accuracy of information, performance and speed of the processes, overall process quality and customer satisfaction.
MPET ANTWERP, BELGIUM
- Capacity: 9 Million TEU/year
- Quay lenght: 3,700m
- Max draft: 17m
- Quay cranes: 41
- Straddle carriers: 234
- Rail handling cranes: 2
- Reefer connections: 2,564
- TOS: Cosmos/TOS
All 41 cranes equipped with Camco BoxCatcher Crane OCR system